CO2 cleaning is a proven, practical method for removing contaminants from the insulating surfaces of energized electrical equipment rated at up to 34.5 kV. Contaminants such as dust, salt spray, dirt, and ash can significantly reduce the dielectric strength of insulating materials. These contaminants can cause increased levels of leakage current to pass over dielectric materials, leading to electrical breakdown due to surface tracking. Such conditions can result in flashovers, which often damage electrical equipment and cause unplanned service outages, as well as safety concerns. CO2 cleaning has been shown to reduce leakage current by more than 96%.
The CO2 cleaning process uses solid CO2 (dry ice shavings or pellets), projected through an insulated wand at a specific nozzle pressure. These high-density dry ice particles (approximately the size of salt granules) are rapidly accelerated using compressed air through a dry air blast line, which requires a compressor that can deliver 150 pounds per square inch (PSI) of pressure at a flow rate of 350 cubic feet per minute. When the CO2 particles strike a contaminated equipment surface, the impact removes the surface contaminants without damaging insulating or underlying materials.
How CO2 Cleaning Works
On impact with the equipment surface being cleaned, the CO2 undergoes sublimation, transitioning from the solid phase to the gaseous phase, without passing through an intermediate liquid phase. The cleaning process works in three different ways:
- Thermal-shock effect: The sudden temperature difference between the CO2 particles (–109.5 °F) and the insulating surface weakens the bond that holds the contaminant intact, causing it to break apart.
- Thermal-kinetic effect: During sublimation, the CO2 gas expands, lifting the remaining contaminants from the insulating surface.
- Kinetic energy: The accelerated CO2 blows contaminants off of insulating surfaces
CO2 cleaning is non-toxic and does not produce secondary waste; only the lifted contaminants fall from equipment surfaces. CO2 is also non-conductive, which allows cleaning of many types of energized electrical equipment (rated at up to 34.5 kV), including overhead and underground distribution switching equipment; metal-enclosed switchgear for indoor and outdoor distribution; distribution transformers; substation power transformers, circuit breakers, and buses; and other equipment prone to contamination. Unlike other cleaning methods, such as water blasting and cleaning with solvents, CO2 cleaning does not require equipment de-energization and grounding; it allows electrical equipment to be cleaned without a planned outage.
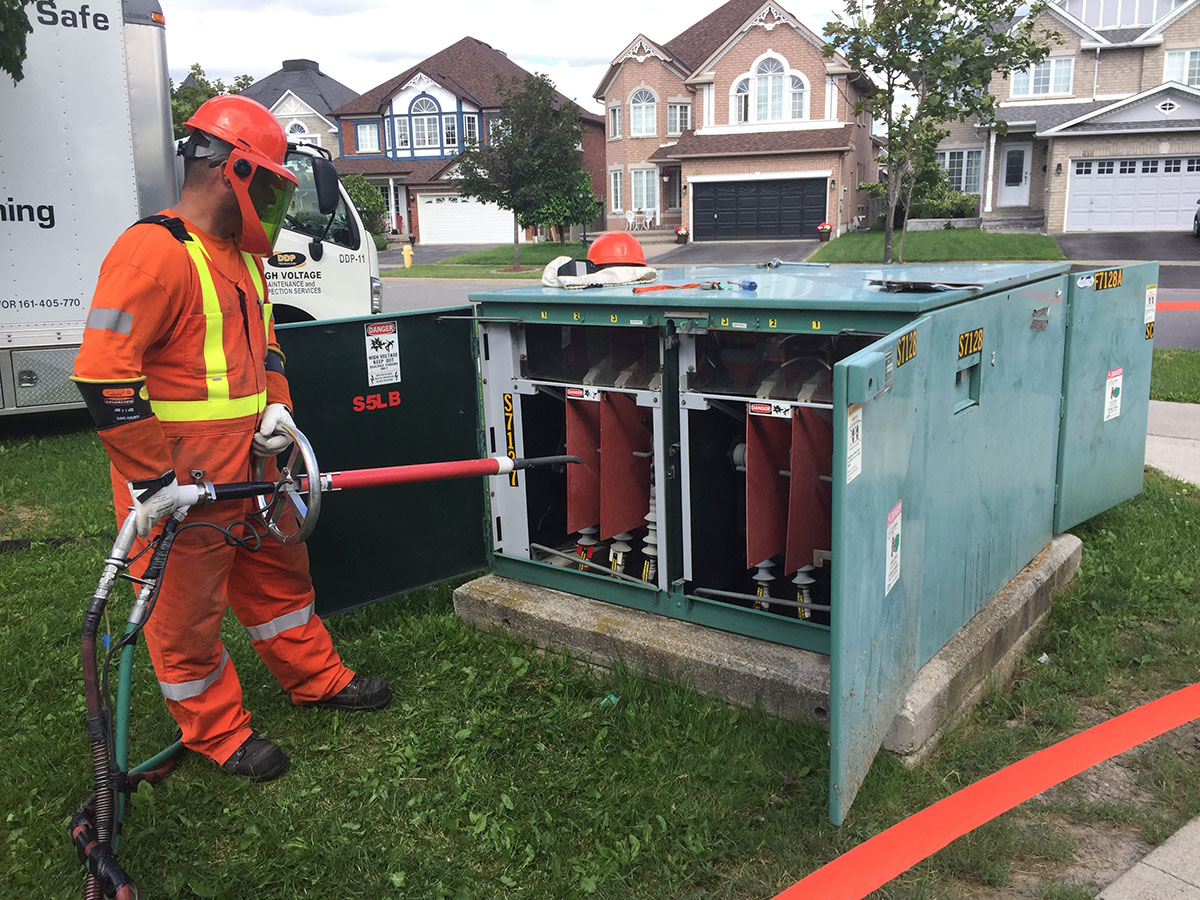
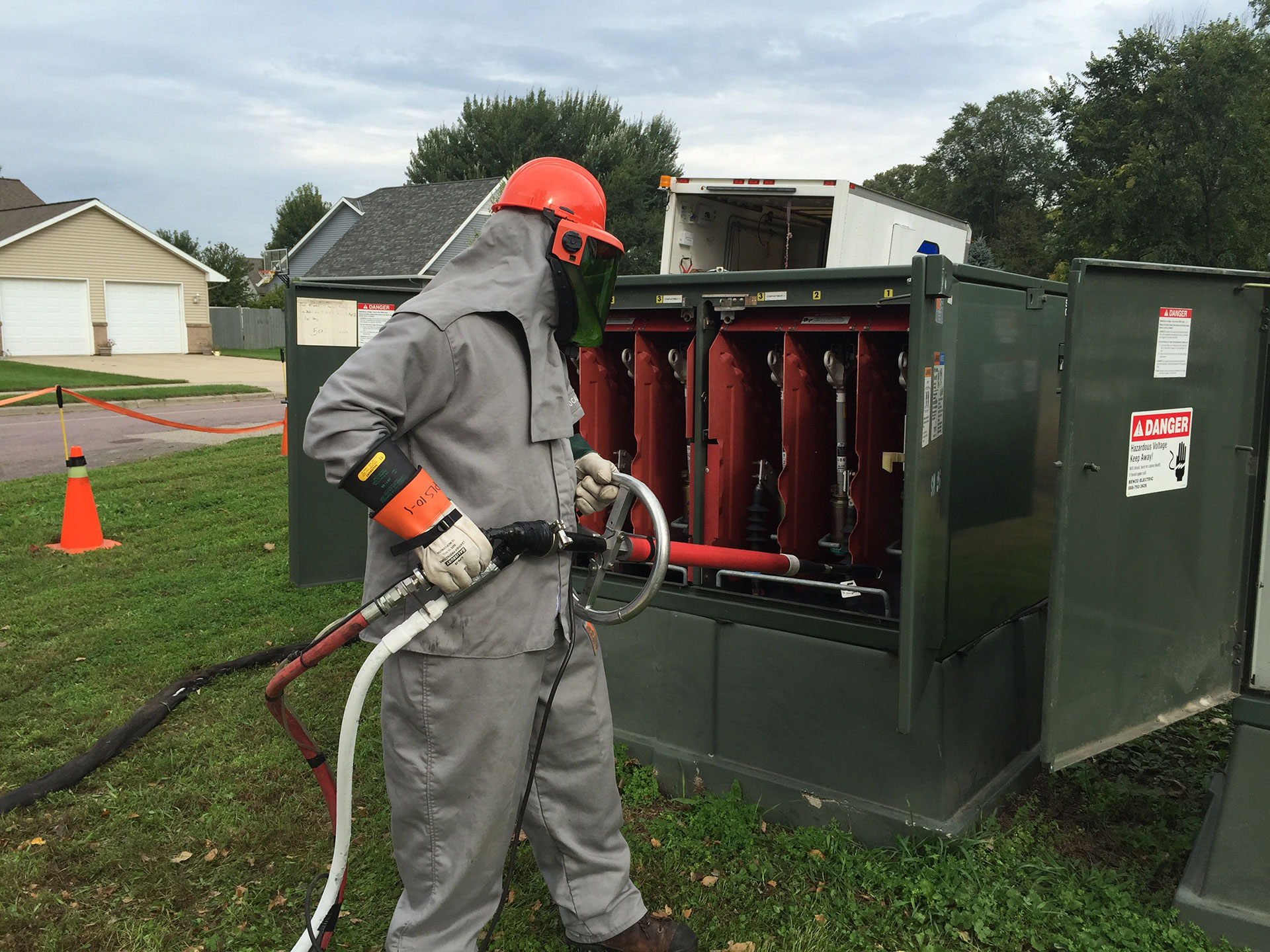
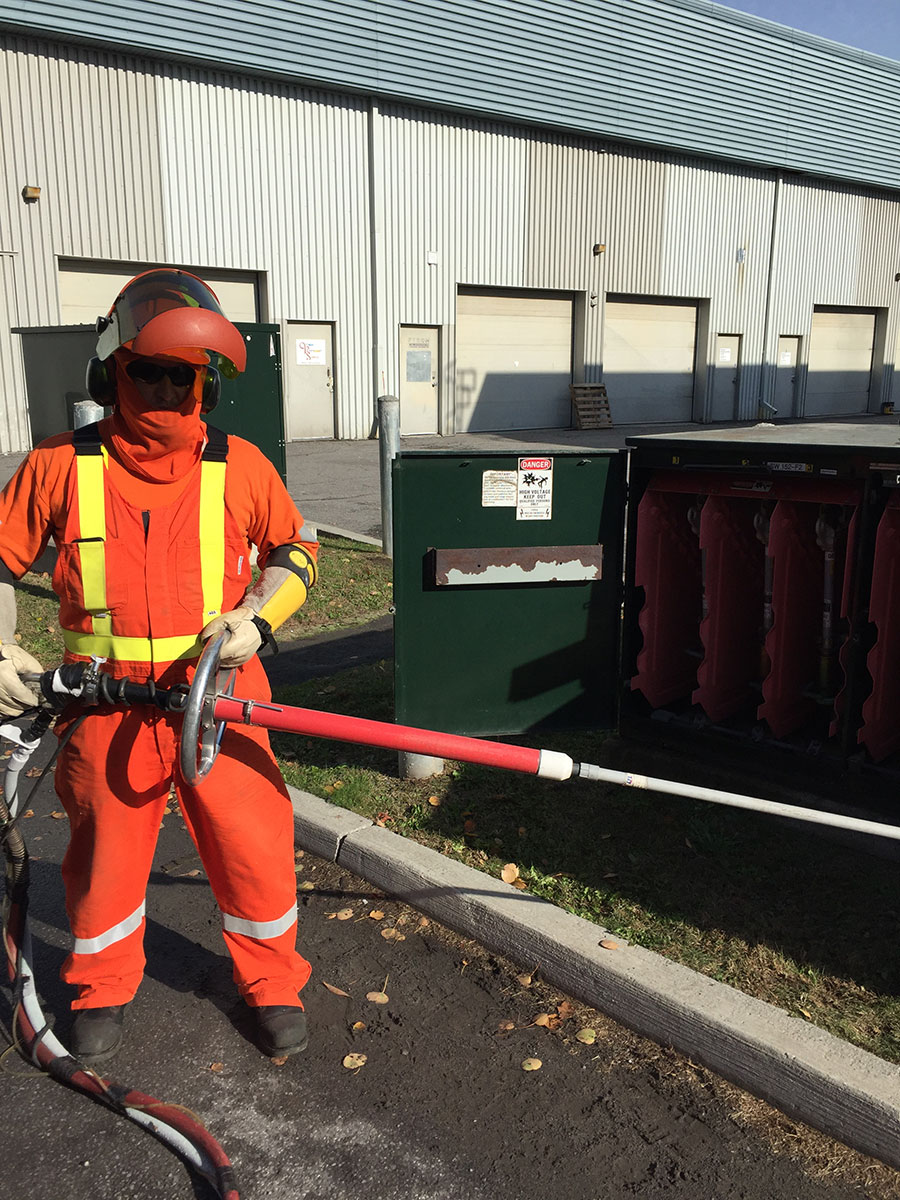
DDP’s CO2 Cleaning Services
As part of an overall asset management program, CO2 Cleaning Services are intended for routine maintenance of electrical equipment.
CO2 Cleaning Services are particularly beneficial for equipment exposed to harsh conditions in coastal regions and high traffic volume areas, high-humidity areas, and other contamination-prone environments. With routine CO2 cleaning, costly equipment flashovers can be significantly reduced in any environment, and equipment life can be extended. In addition, the supply of CO2 is recycled from other industry processes, making it an environmentally friendly option.
CO2 cleaning is the only method that allows cleaning of energized equipment without generating secondary waste, saving the time, costs, and labor associated with planned outages. With reduced set-up and take-down times, CO2 cleaning enables the cleaning of more equipment in one day than other methods.
Working with utilities, DDP estimated the substantial cost savings CO2 Cleaning Services can provide over current methods. Because CO2 cleaning does not require an outage, it eliminates the need for technicians to de-energize and re-energize equipment and prevents utility revenue losses due to outages, which can cost on average $1,000 per hour for each piece of equipment taken out of service. When all costs are considered, DDP’s CO2 Cleaning Services can provide utilities with a typical cost savings of more than 60% over their current cleaning method. If there is no current cleaning method used to maintain equipment, this can cause tracking to develop and could eventually lead to a flash-over in the equipment causing an unexpected outage.
Before performing CO2 cleaning, DDP conducts a complete equipment safety inspection, establishes a clearly defined safety perimeter and signage, and provides immediate support if equipment is determined unsafe to clean or requires repair. DDP provides detailed equipment condition inspection reports, which frequently meet routine maintenance mandates in some states. DDP’s team of extensively trained Power Systems field technicians wear appropriate personal protective equipment (PPE) and adhere to DDP’s safety procedures while cleaning energized electrical equipment.
DDP uses proven safety protocols for CO2 cleaning.
High-Voltage Dry Ice Cleaning
Cleaning the rear of the insulators
High-Voltage Dry Ice Cleaning
Electrical Vault Room Cleaning
High-Voltage Dry Ice Cleaning
Live Termination Cleaning
High-Voltage Dry Ice Cleaning
This video illustrates the effective cleaning power of Dry Ice